生産性向上は、企業の競争力を維持するために欠かせません。しかし、現場では「何から始めればいいのか分からない」「改善しても効果が見えにくい」などの悩みを抱えることが多いです。
本記事では、生産改善に役立つ5つの手法を紹介し、現場ですぐに実践できるポイントを解説します。まずは生産改善の基本から確認し、自社に適した手法を見つけてください。
生産改善が必要な理由とは?競争激化とコスト削減
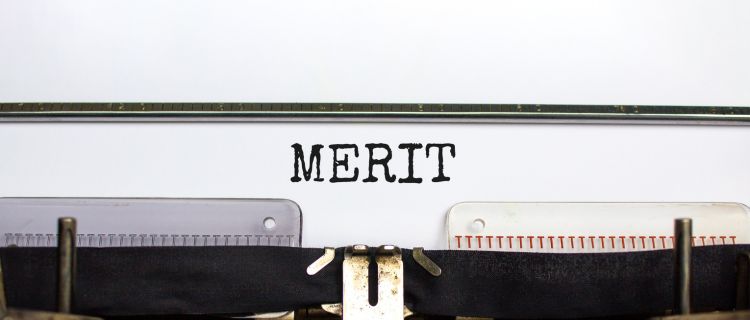
市場競争が激化する中で、企業はどのように生き残るべきでしょうか?ただ仕事をこなすだけでは、競争に勝ち抜くことは難しいでしょう。競争力を維持するためには、効率的な生産体制を構築することが不可欠です。これからの時代、無駄を減らし、改善を続けることが成功を促進する要因です。
次の見出しでは、競争の激化とコスト削減の観点から、なぜ生産改善が必要なのかを解説します。
競争激化に対応するための競争力の維持
近年、グローバル化が進む中で市場競争はますます激化しています。特に日本では、労働力人口の減少が顕著であり、限られた人材で高い生産性を実現することが急務です。生産改善を進めることで、限られたリソースを効率的に活用し、競争力を確保することが可能になります。
さらに、国際市場での競争力を高めるためには、品質を保ちながらもコストを削減する工夫が必要です。持続的な改善が、今後の競争に勝ち残るための重要な要素となるでしょう。
コスト削減を進めるため無駄を削減し利益を最大化
コスト削減を進め、利益を最大化するためには、生産改善の視点を持つことが重要です。単なる原価削減だけではなく、業務全体を見直し、効率的な手法で品質と納期を守りつつ、コストを削減することが大切です。
特に国内生産では、「品質(Q)」「コスト(C)」「納期(D)」のバランスを取ることが求められます。ムダ排除、技術導入による継続的改善で、競争力向上と利益最大化が可能です。
品質向上と従業員負担軽減が作業効率と品質を両立する
生産改善を進める上で、品質向上と従業員負担軽減は大切です。業務のムダを減らすことで、作業の統一化が進み、誰が作業をしても一定の品質を保つことができます。
さらに、機械の導入により作業員ごとの技術差をなくし、人的ミスも減らすことが可能です。これによって、品質の安定とともに、従業員の負担も軽減され、作業の効率化が進みます。結果的に、生産性の向上が期待でき、職場全体の雰囲気も良くなるでしょう。
生産改善の効果とは?業務効率化とモチベーション向上
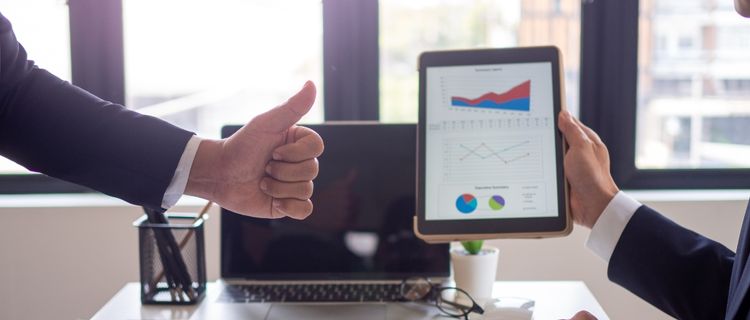
生産改善を進めることで、どのような効果が期待できるのでしょうか?実は、業務効率化だけでなく、従業員のモチベーション向上にも大きく貢献します。無駄な作業を減らし、効率的なプロセスを導入することで、作業負担が軽減され、仕事の質が向上します。
これにより、企業全体の生産性が向上し、良い結果が得られるでしょう。次の見出しでは、実際にどのような効果があるのか、具体的に解説します。
従業員教育で生産性向上!モチベーションが左右する
従業員の能力を向上させることで、業務の統一化が進み、不要な作業を削減できます。実務を通じた指導と研修を取り入れることで、業務の効率が向上し、PDCAサイクルを活用した継続的な改善が可能です。
さらに、教育の充実は従業員の意欲向上にもつながり、離職の抑制と職場環境の向上にも貢献します。
『見える化』で生産現場を効率化
生産改善に「見える化」を導入することで、さまざまなメリットが得られます。生産プロセスをリアルタイムで把握できるため、非効率な工程を素早く特定し、改善につなげることができます。また、在庫と生産状況を可視化することで、余分な在庫の発生と欠品を防ぎ、より的確な生産計画を立てることが可能です。
さらに、データを活用することで問題を早期に発見し、迅速な対応ができるため、品質向上にも貢献します。こうした取り組みを重ねることで、生産性が向上し、コストの最適化にもつながるでしょう。
生産改善を実現するための5つの手法
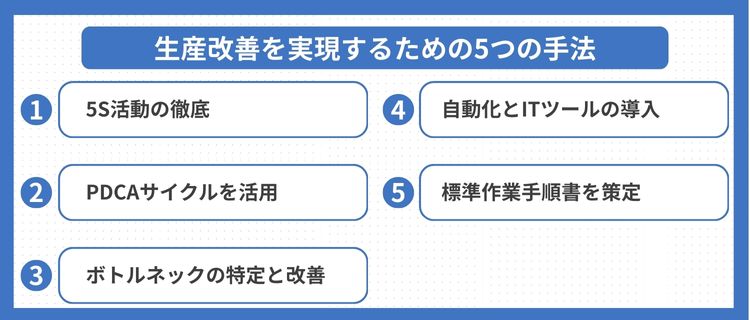
生産改善を進めるには、どの手法を選ぶべきか悩むこともあるでしょう。実際に現場で使える手法を選ぶことが、改善を成功に導くポイントです。例えば、5S活動やPDCAサイクル、ボトルネックの改善など、効果的な手法を組み合わせます。そうすることで、業務効率を高め、コスト削減と品質向上が可能になります。
次の見出しでは、これらの手法を実践する方法を詳しく見ていきましょう。
1.5S活動を徹底する
生産改善の基礎となるのが5S活動です。「整理」「整頓」「清掃」「清潔」「しつけ」を徹底することで、作業効率を高め、職場環境を改善できます。不要なものを排除し、必要な道具を定位置に配置することでムダな動きを削減可能です。
さらに、清掃と清潔を習慣化することで、故障と事故のリスクを低減でき、安定した生産体制を維持しやすくなります。従業員への教育を継続し、5Sを根付かせることで、効率化と品質向上を実現し、生産改善を促進することができるでしょう。
2.PDCAサイクルを活用する
生産の改善を持続的に進めるためには、PDCAサイクルを活用するのが効果的です。PDCAとは「計画(Plan)」「実行(Do)」「評価(Check)」「改善(Action)」を繰り返す手法です。これにより、業務の精度を高めることが可能です。
例えば、作業手順を見直してムダを削減する計画を立て、実施後に成果を数値で分析します。その結果をもとに課題を特定し、さらに改善策を加えることで、業務の効率が向上します。このプロセスを継続することで、生産改善を確実に進めることが可能です。
3.ボトルネックを特定し改善する
生産改善を進めるには、製造ラインの課題を正確に把握し、最適な方法で対処することが大切です。特に、作業の遅れと非効率を生む「ボトルネック」の特定が重要になります。
まず、生産プロセスを詳細に可視化し、どの工程に問題があるのかを明確にします。フローチャート・データ分析を活用し、無駄な作業を洗い出しましょう。その後、工程の見直しと自動化を取り入れ、継続的な改善を実施することで、生産効率の向上と安定した業務運営が可能になります。
4.自動化とITツールの導入
生産改善を実現するためには、業務のデジタル化と自動化を取り入れることが有効です。従来の手作業をシステム化することで、業務の効率が向上し、作業ミスの発生を防げます。例えば、在庫管理システムを導入すれば、現在の生産状況をリアルタイムで把握し、過不足なく資材を調達できます。
また、RPAを活用すれば、データ入力と確認作業の自動化により、人的負担を軽減可能です。これらの改善策を導入することで、生産性向上と業務の最適化を同時に実現できるでしょう。
5.標準作業手順書(SOP)を策定する
生産改善を進めるためには、作業の標準化が不可欠です。標準作業手順書(SOP)を整備することで、作業のバラつきをなくし、誰が担当しても一定の品質を保つことができます。業務の属人化を防ぐためにも、明確なマニュアルの作成が重要です。これにより、新人教育の負担を軽減しながら、業務の効率化と品質の安定化が可能になります。
さらに、イレギュラー対応の手順も明文化することで、トラブル発生時の迅速な対応が可能になり、生産性の向上につながります。
生産改善を実施するためのステップ
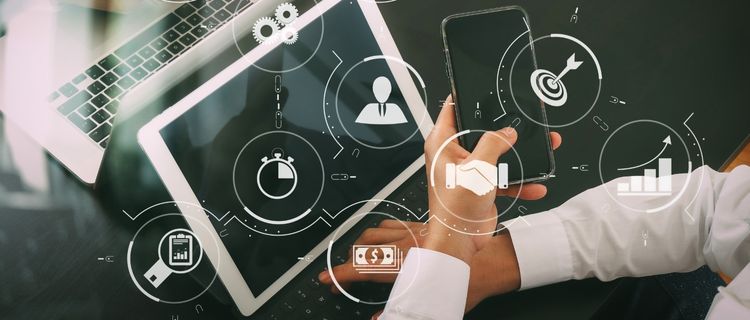
生産改善を進めるには、どこから始めればよいのでしょうか?それにはまず、現状分析を行い、課題を明確にすることが重要です。その後、目標を設定し、適切な改善手法を選んで導入します。改善策を実施後は、その成果を評価し、継続的に改善を行うことで効率化が進みます。
これを繰り返すことで、生産性を向上させ、業務の最適化を実現可能です。次の見出しでは、これらの改善ステップを詳しく見ていきましょう。
1.現状分析と課題の明確化
生産改善を進めるには、現状を分析し、課題を明確にすることが重要です。作業の流れをフローチャートで整理し、ムダと非効率な部分を洗い出しましょう。問題の根本原因を探る「なぜなぜ分析」を活用すれば、改善の方向性が明確になります。
さらに、「QC7つ道具」を使えば、パレート図や特性要因図などのデータを基に、品質問題を客観的に捉え、適切な改善策を導き出せます。これにより、継続的な生産改善が可能です。
2.改善目標を設定
生産改善を効果的に進めるためには、具体的な目標を設定することが欠かせません。改善の方向性を明確にし、数値を用いた指標を設けることで、進捗を把握しやすくなります。例えば、「材料在庫を適正化する」場合、最適な在庫量を設定し、仕入れ計画を見直すことが求められます。
また、達成困難な目標ではなく、実現可能な範囲で計画を立て、定期的に見直すことが重要です。適切な目標と手法を組み合わせ、着実に生産性を向上させましょう。
3.改善手法の選定と導入
生産改善を進めるためには、効果的な手法を選び、段階的に導入することが大切です。最初に、課題に最適なツールと改善策を選定し、まずは試験的に導入してみましょう。例えば、在庫管理の効率化にはITツール、作業ミスの減少にはマニュアルの標準化が有効です。
ただし、全ての工程で1度に導入するのではなく、試運転を行い、その結果を評価した後に本格導入することが重要です。適切な手法を選んで、着実に改善を進めていきましょう。
4.結果の評価と継続的改善
生産改善は1度きりの取り組みではなく、常に見直しを行いながら進めることが重要です。改善の効果を評価し、さらに向上を目指していきましょう。PDCAサイクルを効果的に活用すれば、進捗を監視しながら、精度を高めることができます。また、市場の変動と技術の進展に対応するためには、改善を継続的に行う必要があります。
評価と改善を繰り返しながら、持続的な生産改善を実現しましょう。
生産改善を成功させるための3つのポイント
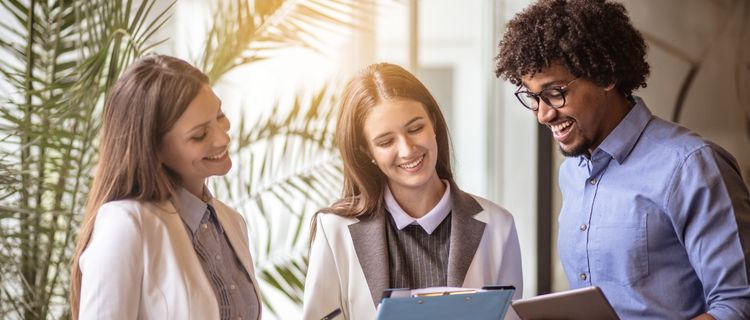
では、生活改善を成功させるためには、どのようにすればよいのでしょうか?まず、達成可能な目標を設定し、進捗を管理することが重要です。次に、現場の意見を反映させ、実行しやすい手法を導入します。
PDCAサイクルを活用し、定期的に見直しを行い、持続的に生産性向上を目指しましょう。次の見出しでは、これらの生産改善を成功させるための3つのポイントを詳しく紹介します。
1.目標設定とチーム協力の重要性
生産改善を効果的に進めるには、明確な目標の設定とチーム全体の協力が不可欠です。目標は具体的かつ達成可能な数値に基づいて設定し、現場の意見を反映させることが大切です。過度な目標設定は逆にモチベーションを下げる原因となるため、適切に調整しましょう。
また、改善活動はチーム全員で共有し、経営層と従業員が一丸となって同じ方向を目指すことが重要です。全体最適を意識し、効果的な手法を導入することで、持続的な改善を実現できます。
2.継続的な改善とフィードバック
生産改善は1度の施策で終わるものではなく、継続的に見直しを行うことが重要です。改善の成果を評価し、さらに効率を高めるためにPDCAサイクルを活用しましょう。小さな改善を積み重ねることで、大きな成果につながります。
また、フィードバックを取り入れながら、変化する市場と技術の進歩にも柔軟に対応することが求められます。定期的な振り返りを行い、持続的な生産改善を実現しましょう。
3.現場の意見を反映する
生産改善を効果的に進めるためには、現場の声を反映させることが重要です。一方的に改善策を押し付けると、作業員のモチベーションが下がり、改善の定着が難しくなります。現場で抱える問題をしっかり把握し、作業の負担が増えないように改善策を考えることが必要です。
また、働きやすい環境を整備し、意見を積極的に取り入れる仕組みを作ることで、持続的な改善を実現できます。現場の意見を反映させ、実効性のある改善を進めましょう。
生産改善のご相談は『CLOUD BUDDY』へ
「生産改善を進めたいけど、どこから手をつければいいのかわからない…。」そんなお悩みはありませんか?『CLOUD BUDDY』は、クラウド型の業務整理・業務処理サービスを提供し、現場の効率化をサポートします。単純作業の負担を減らし、本来の業務に集中できる環境を整えることで、業務全体の最適化が可能です。
導入もスムーズで、小規模な改善から始められます。まずは公式サイトでサービス内容をチェックし、無料相談をご活用ください。
まとめ|激化する競争を生き抜くため生産改善しよう
生産性向上のためには、5S活動、PDCAサイクル、ボトルネックの解消、ITツールの導入、標準作業手順書(SOP)の策定など、適切な生産改善の手法を実践することが重要です。これらを継続的に行うことで、業務の効率化とコスト削減が実現できます。
しかし、現場だけで改善を進めるのは難しいものです。『CLOUD BUDDY』は、業務の整理と処理をスムーズに行え、負担を軽減することができます。『CLOUD BUDDY』のようなサービスを活用して、持続的な成長を目指しましょう。